Bus Bars
CEI’s Power System Division understands the electrical, thermal and mechanical challenges engineers encounter. We specialize in the design and manufacture of insulated bus bars, bus bar assemblies and integrated energy storage solutions that address these concerns. Our products are used in industrial motor drives, conventional or renewable energy generation, power conditioning, distribution and conversion as well as military and aerospace systems.
Benefits:
-
Low Inductance
-
Lower Total Cost
-
Increase System Density
-
Error Proof Installation
-
Structural Support for Additional Components
-
Low Voltage Drop
-
Reduced System Noise
-
Improved Electrical Performance
-
Predictable Performance
-
Cooler Running than Cabling
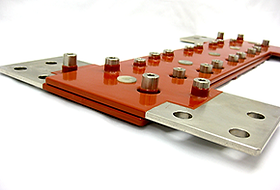
Bus Bar Types

Single Insulated Conductor
​
Custom-machined, formed and plated conductors
Bushings, connectors, other special hardware installed by press fitting or soldering
Powder coated or heat-shrink insulation
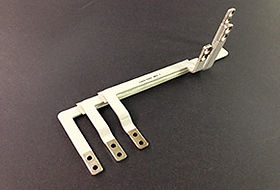
Multi-layer Conductor
​
Two or more conductors insulated from one another by dielectric material:
-
Mylar®
-
Kapton®
-
Nomex®
-
G10
-
Custom shaped / formed then bonded together using adhesive and/or mechanical system
-
Variety of bushings, connectors and other hardware installed

Integrated Electronic Assemblies
​
Mulit-layer bus bar assembly combined with a group of CEI film capacitors
​
Designed and manufactured to meet customer’s specific electrical, mechanical, and environmental requirements
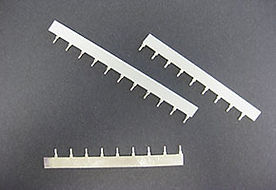
PCB StrongBar Stiffeners
​
Available in any length and various heights
​
Can be used as ground and/or power distribution bus bars (up to 64 Amps) eliminating need for heavy traces
​
Significantly stiffens PCB’s helping the laminated dielectric support its components
Bus Bar Capabilities
CEI knows how critical timely design validation is in product development. Our team is dedicated to assist you in selecting the most technical and cost effective solutions – while maintaining a responsive schedule!
-
3-Dimensional Printing / Prototyping (Fused Deposition Modeling)
-
Component Integration
-
Large Scale Epoxy Vacuum Molding
-
Multi-layer Laminations
-
Mylar®
-
Nomex®
-
Kapton®
-
G10
-
High Dielectric Strength Powder Coating
-
Fluidized Bed and Electro-Static Spray
-
Dielectric Strength of 800v/mil
-
Thickness from .003” to .060”

-
Electrical and Environmental Testing
-
Partial Discharge to 20kVAC
-
Dielectric Withstanding Voltage to 75kV
-
High Accuracy Insulation Resistance & Leakage
-
Semiconductor Dynamic Testing (Switching)
-
X-Ray
-
Simulated High Altitude Testing to 70,000ft
-
Thermal Cycling & Thermal Shock -65°C to +200°C
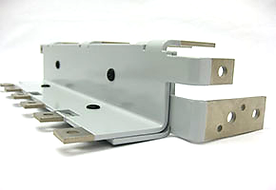